Recent Projects
The Hanford Maintenance Leadership Team Building project Executive Consulting
Polestar provided key personnel and expertise to the Maintenance Leadership Team for one of the prime contractors for the U.S. Department of Energy (DOE) at the Hanford Site near Richland, WA for the purpose of assessing the current status of the Maintenance organizations effectiveness, teamwork, and the progress towards the objectives that the Maintenance Manager has set for the Maintenance Leadership Team. The primary focus of the project would be to:
- Improve communications
- Breakdown barriers
- Modify behaviors
- Unify employees toward a common set of norms for team dynamics
- (Impart) a process to focus the MLT on achieving the goals of the organization
The prime contractor for the U.S. Department of Energy (DOE) responsible for the safe and efficient management, retrieval and treatment of Hanford’s radioactive and hazardous tank waste, preparing it for delivery to the Waste Treatment Plant (WTP) and protecting the nearby Columbia River. The Maintenance organization is responsible for repairs, preventative and corrective maintenance, performing system modifications for the Waste Treatment Plant, and creating work packages that support the work the organization performs in accordance with the Integrated Safety Management System (ISMS).
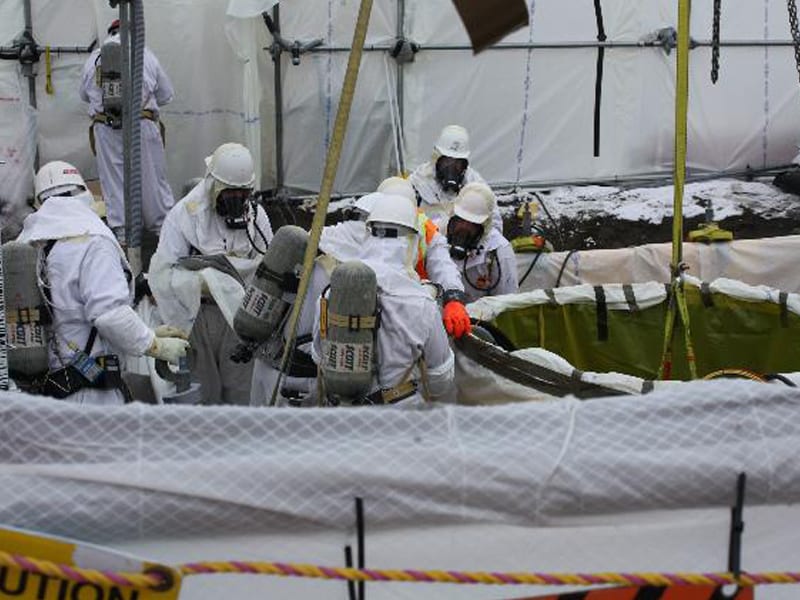
Process
Utimately, the vision of the Maintenance Manager was to create an organization where people are happy to come to work every day and to build an organization with a sustainable culture that carries on good practices that support the mission in a safe and effective manner.
The Polestar team has performed this work in five phases, using surveys, interviews, team meetings and workshops. The five phases consisted of:
Phase 1 was to get acquainted with the organization and understand existing team dynamics, as well as organization culture, process, work flows, roles and responsibilities. This was done by gathering data such as organization charts, position descriptions, performance measures, corrective actions, etc.
Phase 2 consisted of using the survey information, interviews and the “Good, Bad and Ugly” responses, three workshops were conducted. Two four hour workshops were conducted for the first line supervisors and one eight hour workshop for the management team. Each workshop consisted of a facilitated session to determine issue priorities identified in Phase I.
Phase 3 consisted of two half day workshops focused on building team strengths and overcoming team weaknesses. A portion of each workshop was also dedicated to providing status on each of the action plans resulting from the Phase 2 workshops.
Phase 4 was establishing the organization’s routine for achieving results. The team met every two weeks in a Project Status Meeting to status action plans, identify new actions, revise priorities and define metrics. Follow-on Project Status Meetings were established as part of routine monitoring of progress.
Phase 5 Polestar moved from a facilitation role to an observer role as the leadership team took on the responsibility for completing the needed actions. Polestar provided meeting notes and monitored their progress.
Summary
In summary, Polestar helped the Maintenance Leadership Team to understand the team dynamics within the MLT, showed the organization their areas of success and opportunities for improvement and established a common set of norms for team dynamics along with a process for achieving organizational goals.